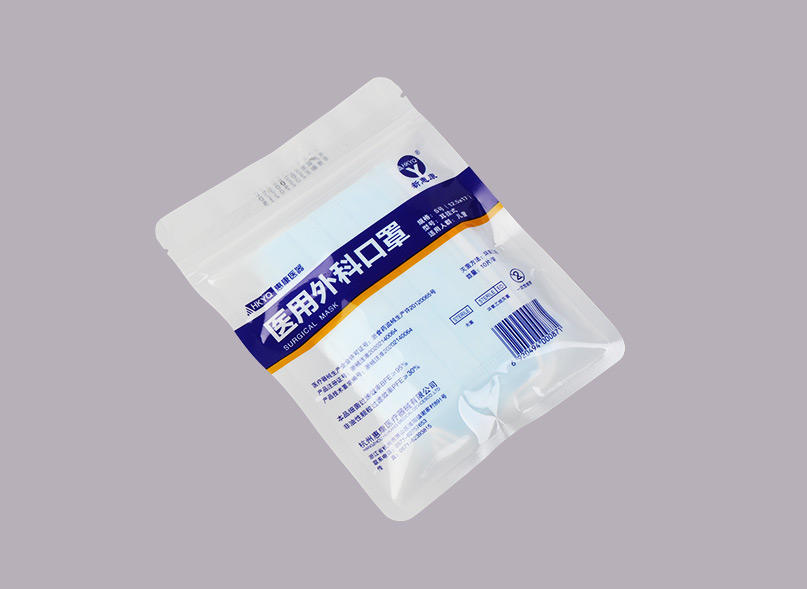
At present, the forming processes of synthetic fiber non-woven filter materials mainly include needle punching, direct injection, bonding, and hot-melting. The hot melt injection molding method is often used. By this method, two or more different fiber materials can be used for composite molding, which improves the dustproof efficiency, and is relatively soft and breathable. The chargeability of the filter material of the dust mask: The size of the two classic filter media belts is positively correlated with the composition efficiency, that is, the larger the electrostatic charge, the higher the dustproof efficiency. When the dust passes through the filter material, the following situations will occur: Collision interception: When the particle size of the dust is larger than the gap between the filter fibers, the dust collides with the surface of the filter material, changes direction due to inertia and force, and settles on the filter surface.
Hooking effect: There are burrs on the fibers. As the dust passes through the filter material, it is hooked by the burrs on the fibers to prevent the penetration of particles. Multi-layer filtration: The filter material is overlapped and woven into a mesh by superfine fibers, which is a multi-layer "three-dimensional structure", and the dust is intercepted layer by layer when passing through the filter material. Electrostatic effect: The filter material has an electrostatic charge, repels dust particles with considerable polarity, and adsorbs dust particles with opposite polarities, that is, captures dust.